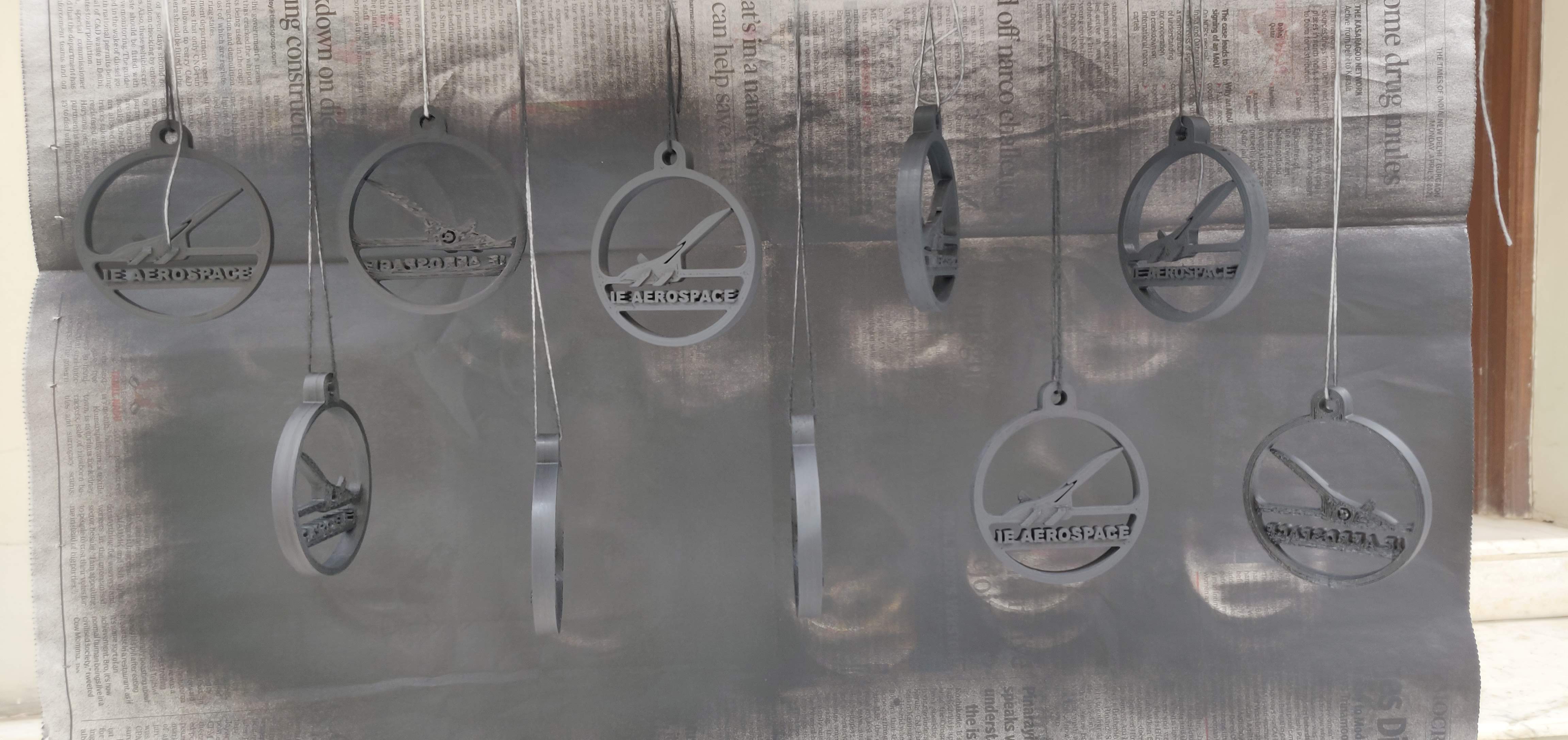
Manipal is home to some of the best project teams in India building innovate products ranging from a solar car to a prototype rocket. After spending two years in the campus of my undergraduate engineering university, I noticed a great need of customized physical parts & products by these student run project teams and clubs of Manipal. Bevel Works was initiated by taking cognizance of this opportunity
With a shared passion, a classmate and I bootstrapped by investing in two 3-D printers and set base at our dorm rooms, turning them into a creative space.
With a mission to deliver high quality products, our job went beyond designing and printing. We spent sleepless nights in sanding and spray painting the prints to provide a polished and professional finish to each printed piece.
To spread the word about Bevel Works, we relied on personal connections and social media. We shared our journey and showcased our creations through word of mouth and Instagram posts.
A lot of our time was spent mastering 3-D printing by troubleshooting printer issues, performing cold pulls to unclog the nozzle, and experimenting with various print settings. Understanding the nuances of bed and nozzle temperatures, fine-tuning print speeds, and optimizing slicer settings allowed us to push our printers to their limits to deliver high quality products.
That being said, one crucial lesson was the importance of setting realistic expectations for the user. we acknowledged inherent limitations of fixed deposition modeling (FDM), such as visible layer lines, low functional temperatures, and varying physical properties owing to being a heterogenous part.